Modular Construction
Unraveling Modular Construction: Volumetric vs. Panelized Approach
Last updated:
March 9, 2025
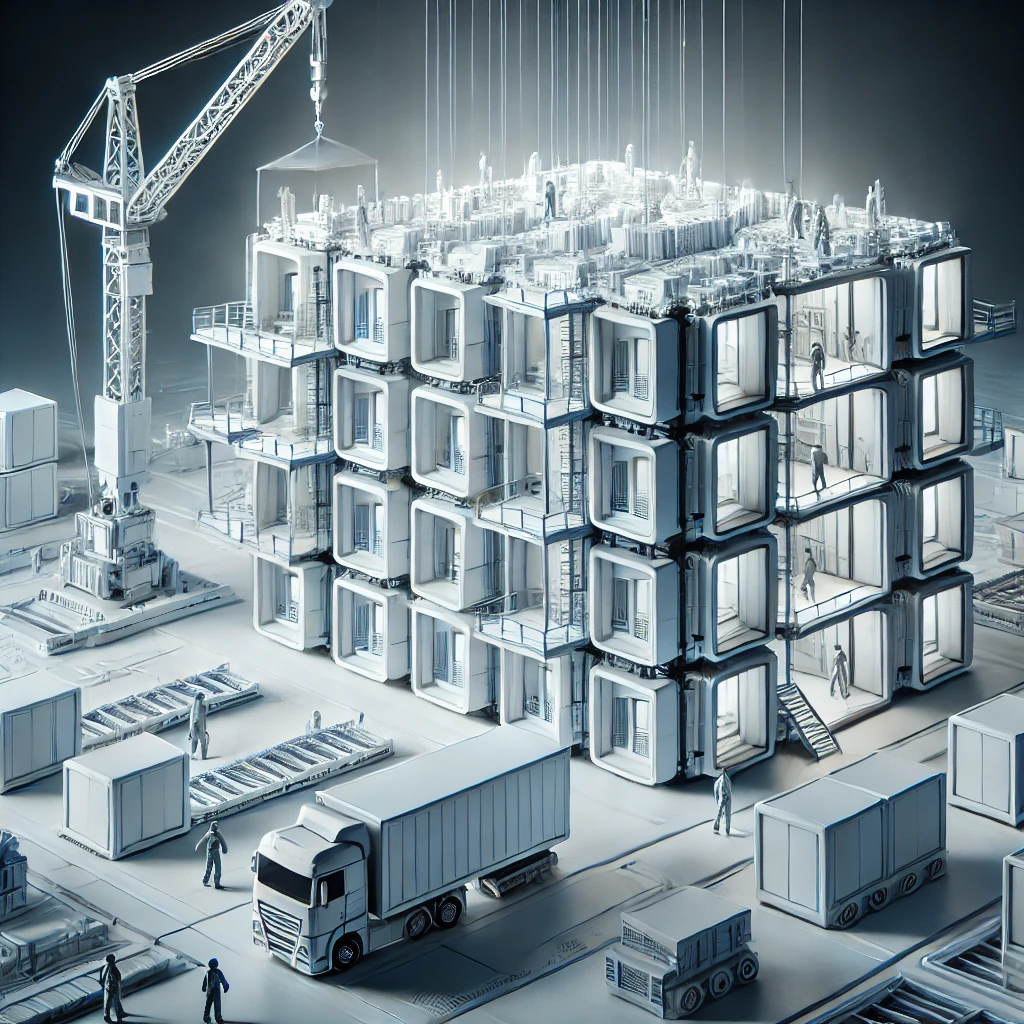
The Future of Construction is Off-Site
Picture yourself walking into a ready-to-move-in apartment that was constructed in a factory, delivered to a location, and piled up like oversized LEGO blocks.
Or envision a home where all the walls, floors, and roofs come separately, waiting to be assembled like a giant puzzle. That's modular construction in action, transforming the way we construct.
With the growing demand for quicker, cheaper, and quality buildings, modular construction is turning out to be the preferred solution.But within this universe, there are two very different approaches—volumetric and panelized construction.
Both have their strengths, weaknesses, and best uses.
Let's break them down and determine which one suits the future of building better.
Understanding Modular Construction
Convention building is like homemade cooking—each step takes place on site and is subject to weather slowdowns, shortages of laborers, and overrunning costs.
Modular building reverses this scenario by moving much of the process off site to an environment controlled in a factory setting.
Modules are built to a high level of precision with waste minimized, efficiency maximized, and the duration of building decreased.
All modular buildings, however, are not created equal. It predominantly resides in two buckets:
- Volumetric building, in which full rooms or a whole section of a building is prefabricated and delivered on site.
- Panelized building, in which floors, walls, and ceilings are made ahead and then bolted together on-site.
Each challenges the traditional means but fulfills various demands. Let us get into both of them.
Volumetric Construction: Building in Boxes
Complete Modules – The Plug-and-Play Model
Consider volumetric construction as sending completely finished hotel rooms directly to the site. Each module is a standalone piece, with walls, floors, ceilings, and even interior components such as lighting, plumbing, and appliances.
Hotels, dorms, and hospitals are typically the types of buildings that take advantage of this method since they need repeated room designs that can be efficiently mass-produced.
Transportation and Installation – Such as Moving Giant Puzzle Pieces
They are built, taken down, and rebuilt to the site where they are stacked or positioned in the required design.
A crane places them in the position, and in a matter of hours, half of the building is already finished.
Sort of like pre-ordering furniture from IKEA, but rather than having to put it together yourself, it comes ready to use.
Speed and Efficiency – Halving Construction Time
Since modules are constructed at the same time while site preparation takes place, volumetric construction severely reduces project schedules.
A structure that could take a year to build conventionally could be delivered in a few months.
That pace was evidenced at its finest during the COVID-19 outbreak when hospitals had to be quickly expanded. Instant healthcare facilities around the globe were offered by modular volumetric units.
Design Constraints – The Trade-Off for Speed
However, there’s a catch. Since these modules have to be transported, they must fit within road and crane size limits. That means less flexibility in design. If you’re looking for large open spaces, complex shapes, or unique architecture, volumetric might not be the best fit.
Panelized Construction: Precision, Piece by Piece
Component Panels – The Modular Puzzle
In contrast to volumetric construction, panelized systems disassemble a building into reduced sections—walls, floors, and ceilings. The parts are pre-fabricated, exported flat, and then assembled on site as a giant puzzle.
Transportation and On-Site Assembly – Easy to Transport, Tougher to Construct
Since panels are smaller than whole modules, they're less cumbersome to ship and can be stacked in an efficient manner. They take more on-site labor than volumetric construction but are still quicker than conventional methods.
Flexibility and Customization – A Designer's Delight
One of the greatest benefits of panelized construction is its flexibility. It gives architects greater design freedom, making it perfect for custom homes and commercial buildings with non-standard floor plans.
Need an open-concept living area or a curved wall? Panelized construction is up to the task.
Less Transportation Complexity – No Oversized Load Permits Required
Because panels are flat-packed, they don't need special transportation planning like volumetric modules do. This makes them perfect for remote-site projects or areas with difficult road access.
Key Differences: Volumetric vs. Panelized
Project Complexity – When to Use Which
If repeatability and speed are the most important factors—such as in hotels, dormitories, and hospitals—volumetric construction is the winner. But for one-off designed spaces that need flexibility, panelized is the solution.
Transportation Logistics – The Problem of Moving Large vs. Small
Volumetric construction has more transportation challenges because whole rooms must be transported. Panelized construction, with its flat-packed modules, is far simpler to transport.
On-Site Customization – Accommodating Change
Volumetric construction leaves little margin for last-minute design adjustments. Panelized construction, on the other hand, permits adjustments in the field, providing builders with greater control over the end result.
The Bottom Line – Build Smarter with Merlin AI
Modular construction is revolutionizing the game—volumetric for speed, panelized for flexibility. Regardless of the method, coordination is paramount.
That's where Merlin AI enters the picture. From design to delivery, Merlin simplifies the whole process, eliminating delays, saving costs, and keeping projects on schedule. Stacking modules or building panels, Merlin makes it easy.
The future of construction isn't merely modular—it's intelligent with Merlin AI. Let's build better, faster, and more efficiently.