Modular Construction
Exploring Prefabrication and Modular Construction: Benefits, Challenges, and Applications
Last updated:
March 8, 2025
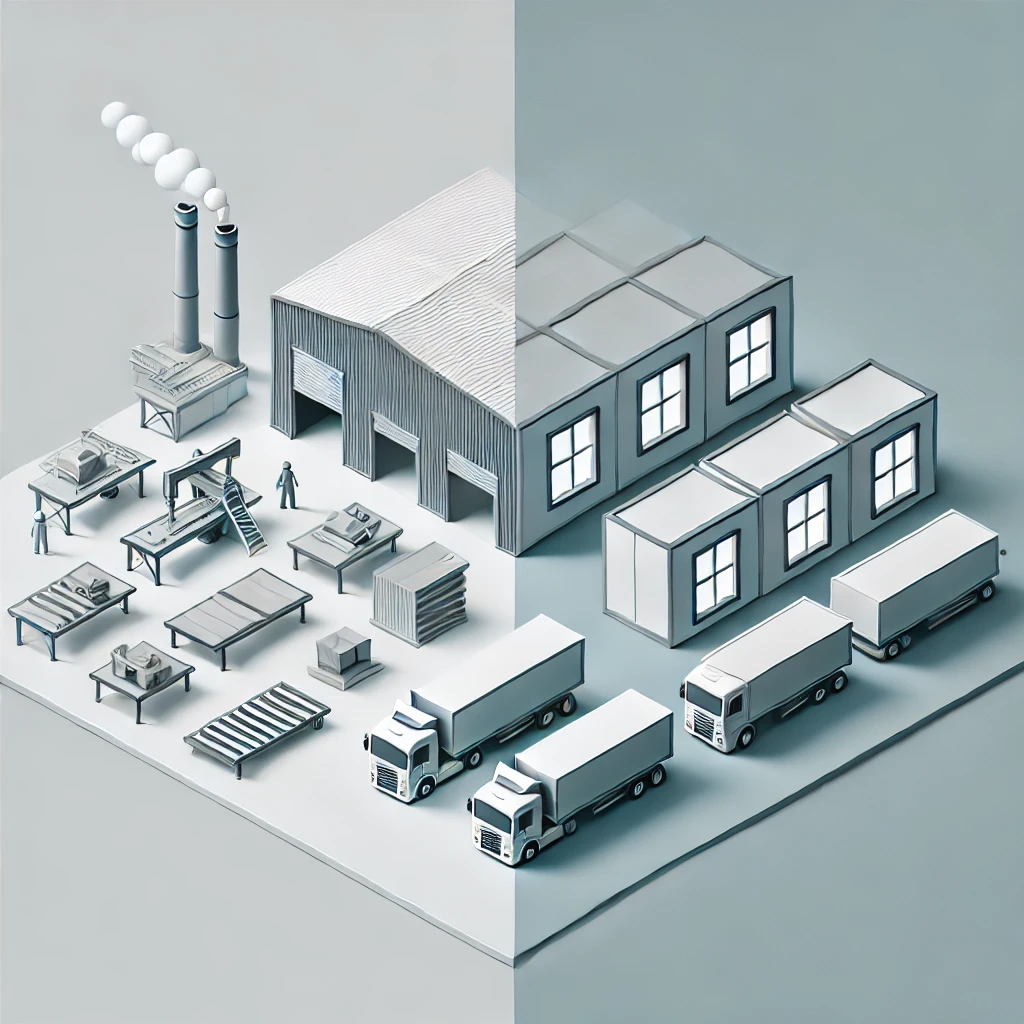
The construction industry is changing. Traditional on-site building methods are being replaced by faster, more efficient, and cost-effective alternatives—prefabrication and modular construction. But what exactly are these methods, and why are they gaining so much attention?
In this blog, we will break down prefabrication and modular construction, including the benefits, challenges, and some real-world applications. Whether you are a developer, contractor, or just curious about the future of construction, this is for you.
What Are Prefabrication and Modular Construction?
Understanding Prefabrication and Its Key Features
Prefabrication refers to the act of manufacturing the building components inside a factory's controlled environment before assembling the components at the construction site. The components could be as simple as wall panels and floor slabs or an entire room.
Key characteristics of prefabrication:
- It reduces on-site labor and minimizes weather-related delays.
- Higher accuracy and quality control in the factory environment.
- It reduces material waste and environmental effects.
Definition of Modular Construction and Its Unique Benefits
Modular construction refers to prefabrication where all the sections or "modules" of a building are constructed outside the site. These modules usually contain complete walls, plumbing, and electrical fittings and are assembled on-site as building blocks.
What sets modular construction apart:
- Modules can be piled and arranged in very complex structures.
- The process permits faster completion of a project but sees simultaneous site work and module fabrication.
- Its cost control is better, courtesy of repeatability designs and logistics streamlining.
Advantages of Prefabrication and Modular Construction
Faster Construction Time and Earlier Project Completion
Modules, as well as building elements, are prefabricated off-site while site groundwork preparation is undertaken, which enables projects to be delivered up to 50 percent faster than traditional construction.
- Workflow parallelism accelerates construction.
- Less exposure to weather-related construction delay
- Construction can be delivered within the timeframe and budget.
Improved Cost Predictability and Budgeting
One of the biggest fears of construction is that it will run over budget. Prefabrication and modular construction can help remove surprise costs in several ways:
- Standardized production minimizes waste from materials.
- Less labor required on-site saves money.
- Better pricing upfront removes financial surprises.
Reduce Material Waste and Environmental Impact
Construction sites generate a lot of waste, from excess materials, packaging, and inefficiency. Prefabrication minimizes this impact in the following ways:
- Precise measurements to minimize waste in material cuts.
- Recycling leftover materials in the factory.
- Reducing on-site emissions through limited work at the construction site.
Enhancing Worker Safety and Productivity
Factory settings present controlled environments that minimize accidents due to:
- Unpredictable site conditions and adverse weather.
- Heavy lifting and dangerous scaffolding operations.
- Congestion and overlapping trades on site.
By taking labor indoors, to a safer and controlled environment, workers are injured less often and are more productive.
Difficulties in Prefabrication and Modular Construction
Over-Engineering and Structural Constraints
Modules need to be strong enough to withstand transportation and lifting, sometimes requiring extra reinforcement. This can lead to:
- Increased costs due to additional structural materials.
- Heavier modules, make transport more challenging.
Applications of Prefabrication and Modular Construction
Residential Housing Projects
Prefabricated homes are changing the housing sector by providing:
- Affordable and scalable housing solutions.
- Rapid assembly, reducing housing shortages.
- Eco-friendly designs that use green materials.
Commercial and Office Facilities
Modular office buildings are becoming popular because:
- Businesses need workspace faster.
- Customized interiors for the specific requirements of a company.
- Expansion and growth at economical costs.
Institutional and Specialized
Hospitals, schools, and military barracks benefit from modular construction in terms of:
- Providing emergency buildings quickly.
- Stricter quality control for safety and durability.
- Causing less dislocation to other communities.
Growth Trends and Regional Insights
Europe: Prefabricated Housing Market Leaders
European countries are at the forefront of modular housing because of:
- Strict sustainability regulations driving the adoption of prefabrication.
- Urban housing demands require faster solutions.
North America: Rising Permanent Modular Opportunities
Permanent modular construction is experiencing growth in both the U.S. and Canada, with more government funding allocated to
- Prefabricated affordable housing
- Increased commercial and healthcare needs for modular construction
Impact of Prefabrication on the Construction Industry
Changes in design practices due to modular limitations
Designers, architects, and engineers are designing to accommodate:
- Modular constraint-friendly designs.
- The use of BIM modeling software to create and refine their designs and planning.
Efficiency Gains in Construction Phases with Factory Environments
Factory-based construction is making site work faster, cleaner, and more precise. This allows:
- Simultaneous construction processes that reduce overall timelines.
- Higher quality finishes than site builds.
The Future of Prefabrication and Modular Construction
Innovations Driving Market Expansion
Advancements in automation, robotics, and 3D printing are driving prefabrication to new levels, allowing for:
- More complex designs to be built off-site.
- Greater precision and customization in modular components.
Sustainable Practices and Long-Term Potential
As sustainability emerges as a main priority, modular construction will be growing by the following:
- Usage of recycled and renewable materials
- Carbon footprint through optimized energy consumption
Final Thoughts
Prefabrication and modular construction are changing the face of future building. Fast timelines, cost savings, and sustainability are good reasons why many companies are taking up these methodologies. However, challenges such as design flexibility and transportation logistics require careful management.
As technology and innovation continue to change, one thing is certain: modular construction is here to stay. For the developer, architect, or builder, embracing prefabrication could be the way forward.